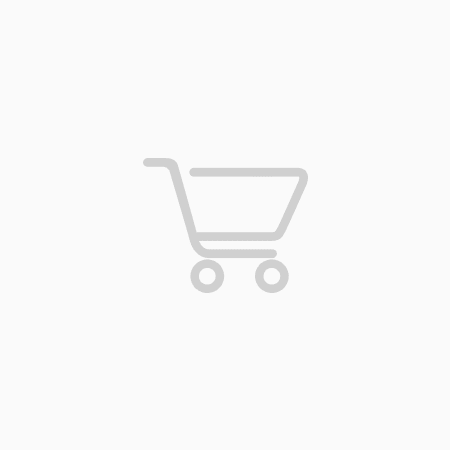
Auger Powder Filling Machine HZF-C
This machine is a complete, economical solution to your filling production line requirements, measuring and filling powder and granule.
Introduction
HZF-C Auger Powder Filling Machine adopts PLC control and hybrid stepping motor drive technology, which is stable and reliable, with repeatability and low noise. The discharge is controlled by the photoelectric switch and is not affected by the environment. The contact with the material is made of high-quality stainless steel material, which has strong corrosion resistance and no pollutants. Only need to replace the metering screw components to achieve different materials, different specifications of filling needs, the entire process is less than 10 minutes.
This machine is a complete, economical solution to your filling production line requirements, measuring and filling powder and granule.
It consists of the Filling head, an independently motorized chain conveyor mounted on a sturdy, stable frame base, and all necessary accessories to reliably move and position containers for filling, dispense the required amount of product, then quickly move the filled containers away to other equipment in your line(e.g., cappers labelers, etc.). It fits more to the fluidic or low-fluidity materials, like milk powder, albumen powder, pharmaceuticals, condiment, solid drink, white sugar, dextrose, coffee, agriculture pesticide granule additive and so on.
This machine is basically configured as a host and a PLC. The host is used to complete the quantitative filling. The PLC is used to store operating instructions such as logic operation, sequence control, timing/counting and arithmetic operations, and control the filling of the machine through digital or analog input and output interfaces. You can also choose automatic feeding device, falling device, etc. according to your needs to further improve efficiency, quantitative accuracy and automation.
The machine has automatic quantitative filling, automatic correction error, material level control, automatic material clearing, calculation and other functions. With high sensitivity, high precision and high reliability, it can meet the filling requirements of different specifications. The machine is used for quantitative filling of uniform granular and small granular materials.
Due to the special professional design, so it is suitable to the fluid or low-fluidity materials, like coffee powder, wheat flour, condiment, solid drink, veterinary drugs, dextrose, pharmaceuticals, powder additive, talcum powder, agriculture pesticide,dyestuff and so on.
Advantage:
Automation
Specifications
Model | HZF-C |
---|---|
Max Capacity | 1500-2500Â bottle/h |
Filling accuracy | 1% |
Dia. Of Bottle | φ20-150mm |
Height of Bottle | 60-300mm |
Power | 1KW |
Voltage | AC220V,50/60HZ |
Dimensions | 900x900x2000mm |
Weight | 380kg |
Remarks
- All stainless steel design(contact part 304SS which is food grade), meet the health-class standards, mainly for pesticides, veterinary drugs, etc.
- The packaging machine of pesticides, veterinary drugs, premixes, additives, milk powder, starch, seasonings, enzyme preparations, fodder, and other powder-like quantitative packings.
structure
Requirements
The ground is level and the environment is kept dry.
The power supply is a two-phase three-wire system. It should be well grounded to ensure safe use.
Do not mix debris in the material and in the hopper of the filling machine.
Security instructions
This product is a precision instrument and must pay attention to the following items during use and transportation:
1. The power supply must be used within the specified limits, in the following range: -15%-10% of rated voltage value 220V, + 2%-2% of rated frequency value 50Hz;
2. Replenish grease to the stirring motor reducer every 10 months.
3. Wipe the machine clean when not in use and place it in a dry and ventilated room.
4. When the machine is working, if the abnormal sound response, immediately cut off the power.
Common fault checking and handling
The screen does not display when you turn it on.
Solution: Check if the power supply is normal; check if the fuse is normal.
Photoelectric switch response is not sensitive.
Solution: It may be caused by the dust on the sensor head being too thick or the sensitivity is too low. Wipe the dust off the photoelectric switch section and increase the sensitivity.
Block the photoelectric switch but do not discharge.
Solution:
- Measure whether the photoelectric switch voltage is normal (should be 12V); measure whether the signal line voltage of the photoelectric switch is normal (about 0V when blocked, and about 11V when not blocked).
- Turn on the electrical box. If the red light on the stepper motor driver indicates that the current voltage is too high, the stepper motor driver protects itself and stops working.
Inaccurate discharge
Solution:
- The material is too wet or agglomerated. The material in the hopper absorbs moisture or the material is agglomerated due to backlog, please clean up the block material.
- The unloading screw is not turning correctly. Please modulate the power line.
- There is foreign matter in the material, and the screw is caught, causing the number of steps to increase and the weight value to decrease. It can be solved by removing foreign matter.
- The stirrer blade is not in the proper position. Adjust the position of the stirring blade to the proper position to solve.
- The stepper motor frequency is not suitable. The frequency is too high. The frequency is too high and the speed is too fast, and the material is not ready to be filled into the hopper in time. Reduce the frequency to solve.
- The operation method is incorrect (such as leaking material or the container is too high to block the hopper, resulting in the material not fully entering the container). According to the correct operation method, it can be solved normally. (Note: When the distance between the workbench and the hopper is too large, the relative position of the unloading screw and the hopper can be adjusted to the best by changing the upper and lower positions of the long axis.)
- The material in the hopper is too small, and it can be solved by feeding to the appropriate position. When the addition amount and the addition speed are too fast, a large amount of material impact is caused, and the instantaneous change of the density is too large to affect the short-term measurement. Increasing the number of feeds, reducing the feed rate and a single addition can be solved.
- The grid voltage is unstable. Add a voltage regulator.
- Nylon pin shear wear is too large. The nylon pin of the coupling is excessively sheared and worn, resulting in an excessively large angle of rotation of the spindle when the machine is stopped. Replace the nylon pin.
- The screw wear is too large. Replace the screw.
The stepping motor is abnormal and the screw does not rotate.
Solution:
- It may be caused by the stepping motor frequency being too high, and the frequency should be reduced.
- The drive is damaged and the drive is replaced.
- There are debris in the hopper, which is the increase of the resistance of the stepping motor, which leads to the loss of the step and the removal of the debris can be solved.
- The actuator voltage is too low, generally about 100 AC. Check if the power is normal.
- The number of frequency bands is too small. Set the number of large frequency bands, generally 20~40.
- Stepper motor demagnetization is serious. The frequency can be reduced, and if the speed is too slow, the stepper motor can be replaced.
The amount of material to be fed is getting less and less so that the spiral is not idling.
Solution: The stirring motor stops or the drive chain falls off. Check if the motor is damaged and the tensioning wheel is loose.
The main power supply is tripped as soon as it is turned on.
Solution: Since the main unit has a single-phase micro-circuit operation, the three-phase load is unbalanced, and the current in the neutral line passes, triggering the leakage protection action. Industrial circuits only need to have an air switch, and the leakage protection can be solved.
The stirring motor cannot be started.
Solution: The AC contactor that starts the stirring motor is controlled by a thermal protector. When the current is too high, the thermal protection starts, and the AC contact is disconnected to protect the stirring motor. After this phenomenon occurs, after the thermal protection is cooled, press the blue button on the thermal protector to work normally.